AMF Zero Positioning System Application Area Report
What is the most important thing for the fixture? Clamping accuracy, clamping force, convenience of changing the clamp... These are the first considerations when we choose to make the fixture.
What does the machine's operator spend a lot of time doing? Replace the fixture (workpiece) and reposition it.
Why do workers not like small batch production? It is very troublesome to change fixtures and reset the machine. Sometimes it takes a long time. If you have to do a few things, you have to reset it. It is really annoying.
What is the machine doing when the worker changes the fixture? Most of the time is invalid and idling. This is really a problem for expensive machine tools. We very much hope to improve the efficiency of machine tools rather than buying more machine tools. We must reduce costs in order to remain competitive.
China's labor costs continue to rise, factories have to raise prices because of the increase in salary expenditures. In addition to buying more high-end machine tools, is there a less costly way to reduce costs?
The replacement of machine tools is a major trend, and machining centers are increasingly replacing traditional machine tools. So the traditional machine tools that are in good condition are eliminated? Is there any way to use the traditional machine tool to be used with the machining center, and the efficiency is still high?
The above problems have revolutionized solutions in Europe: AMF Zero Positioning System.
The AMF zero point positioning system is so simple that as long as the joint on the pallet or workpiece is roughly aligned with the positioner, the joint will automatically find the path and center and slide into the positioner! Small workpieces, large workpieces are also fixed in seconds!
With a zero point positioning system, you can even save up to 90% of the changeover time. Moreover, the replacement of the workpiece to the fixture is off-line operation, the machine has almost no idle time, and the efficiency of the machine tool is greatly improved. For small batches and multiple varieties of production, the benefits are even more obvious.
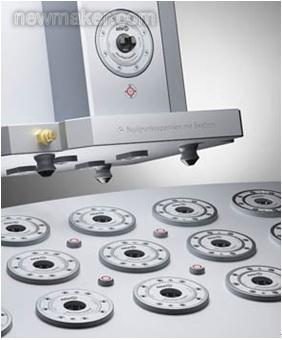
AMF zero point positioning system increases machine work time by 90%
The repeatability of the AMF zero point positioning system is 0.005mm, and the positioning accuracy is very high. Moreover, the AMF zero point positioning system can reduce vibration well, resulting in higher machining accuracy and better consistency. Because of the high processing accuracy, some subsequent processes can even be omitted. The unique self-cleaning system ensures consistent accuracy and maintenance-free operation.
Another benefit of the damping effect is that the life of the tool is suddenly prolonged with the AMF zero point positioning system, which is an important factor in reducing costs.
The AMF Zero Positioning System has distinctive features: full product specifications and high clamping force. From K02 to K40, we are suitable for everything from light to heavy. K02 and K5 are small in size, but also have clamping forces of 6kN and 13kN; K10 clamping force of 25kN can meet the requirements of general machining; K20 and K40 can reach 55kN and 105kN respectively, which is our independence. Some products suitable for heavy cutting are the best choice in the field of heavy cutting.
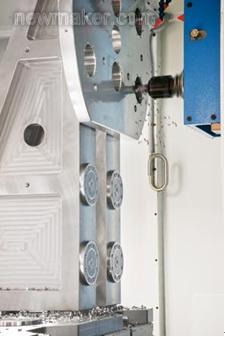
The parts produced by the zero point positioning system have a better surface quality because the clamping system has very good vibration resistance.
The AMF zero point positioning system is available in both hydraulic and pneumatic versions. The new product 4.5bar air system can be used directly from the factory air source, which is very convenient.
It takes some time to accept the zero point positioning system, but once it starts to use, it will often become a strong advocate.
A packaging machine manufacturer in southern Germany has been using the AMF zero point positioning system since 2009. They custom-made filling machines and equipment for the pharmaceutical industry according to customer requirements, and machine parts and brass molds are required on seven four-axis and five-axis machining centers. This involves using the fixture system that comes with the machine table or using the change tray, and some workpieces are also directly clamped. Previously, the use of pliers, multi-station pliers and other auxiliary tools was time-consuming and labor-intensive, and now the AMF zero-point positioning system is magically fast and safe. The shortened tool change time has increased the actual working time of the machine, and the funds originally intended for the purchase of new machining centers have been saved. However, the zero positioning system encountered great resistance at the beginning of the introduction of the factory. The employees were very skeptical about the new clamping system and firmly opposed to replacing the original clamping system with it. Fortunately, the management of the company firmly believes in the huge potential of the zero positioning system, and communicates with all relevant personnel in design, planning, programming and production to understand the new fixture system and ultimately eliminate their doubts. Then the result is: The harsh opponents become enthusiastic advocates. In addition to time and technical benefits, this change has brought unexpected gains: Employees are deeply in love with the zero point positioning system, constantly looking for and developing new applications and technical improvements of the zero point positioning system. This spontaneous power will create more value for the company in the future.
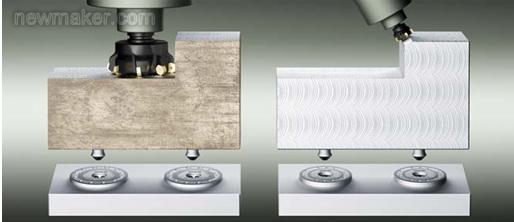
AMF heavy-duty positioning system and universal zero positioning system
Ideal for heavy-duty cutting and light-duty cutting, it has the same interface: AMF universal zero positioner has clamping force 55kN (right) and heavy-duty 105 card N (left) clamping force.
Another German tool manufacturer needs to offer its customers a wide variety of products in different fields, and the batch size is very small. Workers need to replace 3-5 fixtures on a single machine every day. The average time required to change fixtures is 30 minutes. Every machine will be shut down for 1.5~2.5 hours every day because of changing fixtures. Workers need to spend 1.5~ per day. 2.5 hours to debug the tooling, and the replacement tooling requires a high level of worker skill, and the factory needs to spend a lot of manpower and money in this area. To solve this problem, the company introduced the AMF zero point positioning system. Due to the variety of fixtures and large differences, the engineers used the fixture palletization to install each fixture on the pallet. A corresponding number of zero-point positioning joints were installed under the pallets, and a zero-point positioning system was installed on the workbench of each machine. Each fixture has a standardized interface that allows workers to quickly mount to the machine table with high repeatability. The entire process time is very short, and it takes only 20 seconds for some fixtures to be replaced. The company was very surprised by the results, they did not expect to achieve such a good result. Now, the AMF zero point positioning system saves them about two hours each day. The machine can process more products and the workers are easier. The company is no longer worried about some small orders.
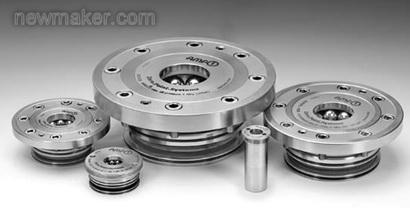
AMF built-in zero positioning system
AMF zero point positioning system is most suitable for small batch flexible parts production or timely production and on-demand manufacturing, workpieces need to be replaced frequently
The benefits of the zero point positioning system make it well deservedly worthy of value.
At present, the AMF zero point positioning system is used in the field of high precision production. In fact, according to the actual situation in China, the use of zero positioning system to combine ordinary machine tools with machining centers is also a good way to save costs and improve efficiency. Of course, the use of zero positioning systems in small batches and multiple varieties of production will bring the greatest benefits.

AMF zero point positioning system for machining heavy workpieces
Reliable clamping even in large-scale heavy-duty machining:
AMF zero point positioning system
Reducing labor costs, improving automation and machining accuracy, this is the development direction of China's machinery processing industry. With the improvement of China's technical level, more varieties of small batches will be produced in the future. The AMF Zero Positioning System will help you move into the future.
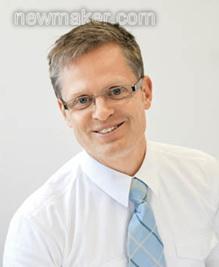
Juergen Foerster, Deputy General Manager of AMF: “When the company's leadership is proactively implemented and all relevant design engineers, solution managers, programming technicians and production personnel are actively involved, the zero positioning system will bring you huge production. to raise efficiency.
Concerned about surprises
Tag: Positioning System AMF Clamping Force Vibrationability Palletization
Previous: Shantui basic components technical transformation project successfully passed the safety Next: Analysis of the influence of milling cutter diameter on the spiral bevel gear teeth
Slotted Channel Unistrut,Channel Unistrut,Slotted Channel Unistrut
Fenghua Jade Motor Co., Ltd. , http://www.steelstructure-supplier.com