Silicon carbide without medium crushing processing line
2022-11-27 14:05:30
I. INTRODUCTION With the development and application of new materials, silicon carbide (sic) materials have a wide range of uses in engineering ceramics, abrasives, refractory materials, chemicals, power, and smelting and foundry industries due to their unique properties. The silicon carbide materials used by domestic and foreign merchants not only have strict requirements on their chemical composition, but also have special requirements on the physical properties and particle shape of the materials. The shape must be a spheroid of equal shape, and there must be no "false particles". "The accumulation exists. Not only is there a strict requirement for its true weight, but there are also strict requirements for the bulk density of materials. Silicon carbide raw materials with low bulk density, poor particle shape, and poor toughness and strength are not competitive in domestic and foreign markets.
Second, the current status of domestic silicon carbide processing and production technology The domestic abrasives industry does not have its own professional processing equipment, generally borrowing mining machinery for crushing operations. At present, the processing equipment and process commonly used for abrasive refractories are: coarse crushing of jaw crusher - crushing of double-roll crusher - fine crushing of ball mill - shaping by wheel dry mill. These processing equipment mainly use the principle of crushing and grinding. Although it can meet the needs of the market within a certain range, it has low work efficiency, large power consumption, poor particle shape, complicated process, difficult equipment maintenance, high cost, and more serious harm in the process of processing broken silicon carbide, due to silicon carbide. The high hardness causes the crusher body to be seriously worn, and the mechanical “iron†brought into the product is particularly large, causing “iron†pollution. The contaminated broken material must be treated with acid washing to remove the “iron†before it can be applied. Not only the processing cost is high, the material loss is large, and it is restricted by the processing technology factors, which affects the processing and production volume, and also causes serious harm to the environment.
Metal iron and its oxides are harmful elements in non-metallic materials. In silicon carbide materials, they also have extremely strict limits, and super-indicators are waste products.
Third, seek scientific and advanced crushing equipment to change the current "iron pollution" processing technology.
Analysis of the traditional processing and crushing process, the process of causing "iron" pollution mainly comes from the "fine crushing" of the ball mill and the "shaping" process of the wheel mill. The silicon carbide with a Mohs hardness of 13 will affect the crusher steel ball and the lining during the grinding process. The board causes severe wear and tear. Generally, the wear and tear of iron is about 2-3 ,. This material cannot be used without acid treatment. Therefore, based on the general situation in the domestic industry, it is urgent to seek a replacement for the traditional crushing equipment. No medium crushing equipment, fundamentally remove the hard index elements such as impurities "iron", and carry out the crushing and shaping integrated fine crushing equipment. The colleagues in the industry have pursued the goal for many years to meet the high-purity silicon carbide materials of the engineering ceramics industry. Requirements. To this end, after a long period of repeated examination and testing, the author believes that the PL vertical impact crusher can fully meet the requirements of pollution caused by the processing equipment itself, such as “iron pollutionâ€, and the shape of the product is good. Shape, bulk density, change the status quo of traditional processing.
PL vertical impact crusher is a new type of crusher for material and material self-impact. It adopts the principle of “stone-rockâ€, which uses the material to accelerate in the impeller when rotating at high speed, and the crushing principle of the material in the vortex chamber of the crusher itself, the material is hardly in contact with the body, which greatly reduces the “iron pollution†of the material. The processed product has a granular shape such as a square shape, and has the dual functions of coarse crushing, fine crushing and shaping.
The traditional use of vertical impact crushers is: processing crushing, aluminum bauxite, refractory materials, steel slag and softer non-metallic materials. The processing capacity is very large and the efficiency is particularly high. However, no one in China has the courage to process the silicon carbide, commonly known as “industrial teethâ€. It cannot be used for reference to technical data and successful experience. With the support of business leaders, In order to be prudent, before the design and finalization of the overall process line, with the assistance of the crusher manufacturer, a total of 80 tons of high-density silicon carbide block material was put into the field for heavy-duty, high-strength industrial tests to identify the machine. The various performances, throughput, wear life of the equipment, as well as production costs and economic benefits.
Specific test process:
Test model PL-700 (supporting motor 55KW)
Test time: June 9-10, 2000 Product structure: 0-5mm mixed sand hourly feed capacity 30 tons output 18.4 tons / hour wear body, runner liner wear consumption is 2kg, processed product 80 Ton.
Average medium "iron" content: 0.002 / 80 = 1 / 40000
Product particle size analysis:
In order to adapt to the market demand for various grain size segments, the frequency converter is used to adjust the motor speed, and the linear speed of the crusher rotor is changed. The product yields of different grain size sections are tested. The yield of different rotor linear velocity products is:
Test conclusion: changing the linear speed of the crusher rotor can change the particle size structure of the product to meet the market demand for different particle size products, so as to reduce the backlog of the product with slow release grain size during the processing.
IV. Design of complete production line After completing the above heavy-duty industrial test, the design of production and production line is carried out.
The processing line is in the form of a space arrangement, and the operation flow is:
The complete set of crushing process is used for closed operation, and the dust collection facility is used for dust collection. The sic content of the processed product is higher than the raw material index Fe2O3 and F•C when the material is fed, which is obviously lower than the raw material index at the time of feeding. (The mechanism is described separately)
After several years of production practice, the production line has stable operation, simple structure, high efficiency and energy saving, high crushing efficiency, fine crushing and medium crushing functions, convenient maintenance and easy operation. Overcoming the traditional processing equipment, low efficiency, serious body wear, difficult maintenance and high cost, greatly reducing the "iron pollution" phenomenon of the material, and the shape of the finished material particles into equal shapes or cubes, no "false" The phenomenon of “particles†has the dual function of “breaking†and “shapingâ€. Basically achieved the purpose of no media processing.
Second, the current status of domestic silicon carbide processing and production technology The domestic abrasives industry does not have its own professional processing equipment, generally borrowing mining machinery for crushing operations. At present, the processing equipment and process commonly used for abrasive refractories are: coarse crushing of jaw crusher - crushing of double-roll crusher - fine crushing of ball mill - shaping by wheel dry mill. These processing equipment mainly use the principle of crushing and grinding. Although it can meet the needs of the market within a certain range, it has low work efficiency, large power consumption, poor particle shape, complicated process, difficult equipment maintenance, high cost, and more serious harm in the process of processing broken silicon carbide, due to silicon carbide. The high hardness causes the crusher body to be seriously worn, and the mechanical “iron†brought into the product is particularly large, causing “iron†pollution. The contaminated broken material must be treated with acid washing to remove the “iron†before it can be applied. Not only the processing cost is high, the material loss is large, and it is restricted by the processing technology factors, which affects the processing and production volume, and also causes serious harm to the environment.
Metal iron and its oxides are harmful elements in non-metallic materials. In silicon carbide materials, they also have extremely strict limits, and super-indicators are waste products.
Third, seek scientific and advanced crushing equipment to change the current "iron pollution" processing technology.
Analysis of the traditional processing and crushing process, the process of causing "iron" pollution mainly comes from the "fine crushing" of the ball mill and the "shaping" process of the wheel mill. The silicon carbide with a Mohs hardness of 13 will affect the crusher steel ball and the lining during the grinding process. The board causes severe wear and tear. Generally, the wear and tear of iron is about 2-3 ,. This material cannot be used without acid treatment. Therefore, based on the general situation in the domestic industry, it is urgent to seek a replacement for the traditional crushing equipment. No medium crushing equipment, fundamentally remove the hard index elements such as impurities "iron", and carry out the crushing and shaping integrated fine crushing equipment. The colleagues in the industry have pursued the goal for many years to meet the high-purity silicon carbide materials of the engineering ceramics industry. Requirements. To this end, after a long period of repeated examination and testing, the author believes that the PL vertical impact crusher can fully meet the requirements of pollution caused by the processing equipment itself, such as “iron pollutionâ€, and the shape of the product is good. Shape, bulk density, change the status quo of traditional processing.
PL vertical impact crusher is a new type of crusher for material and material self-impact. It adopts the principle of “stone-rockâ€, which uses the material to accelerate in the impeller when rotating at high speed, and the crushing principle of the material in the vortex chamber of the crusher itself, the material is hardly in contact with the body, which greatly reduces the “iron pollution†of the material. The processed product has a granular shape such as a square shape, and has the dual functions of coarse crushing, fine crushing and shaping.
The traditional use of vertical impact crushers is: processing crushing, aluminum bauxite, refractory materials, steel slag and softer non-metallic materials. The processing capacity is very large and the efficiency is particularly high. However, no one in China has the courage to process the silicon carbide, commonly known as “industrial teethâ€. It cannot be used for reference to technical data and successful experience. With the support of business leaders, In order to be prudent, before the design and finalization of the overall process line, with the assistance of the crusher manufacturer, a total of 80 tons of high-density silicon carbide block material was put into the field for heavy-duty, high-strength industrial tests to identify the machine. The various performances, throughput, wear life of the equipment, as well as production costs and economic benefits.
Specific test process:
Test model PL-700 (supporting motor 55KW)
Test time: June 9-10, 2000 Product structure: 0-5mm mixed sand hourly feed capacity 30 tons output 18.4 tons / hour wear body, runner liner wear consumption is 2kg, processed product 80 Ton.
Average medium "iron" content: 0.002 / 80 = 1 / 40000
Product particle size analysis:
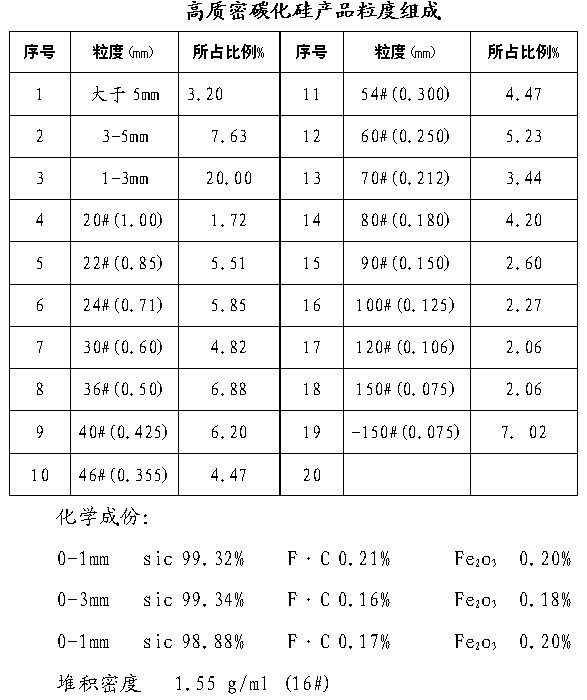
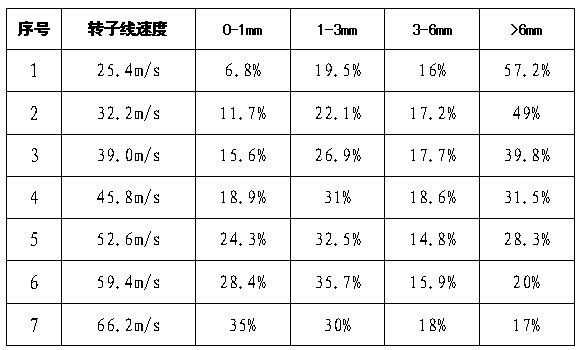
IV. Design of complete production line After completing the above heavy-duty industrial test, the design of production and production line is carried out.
The processing line is in the form of a space arrangement, and the operation flow is:
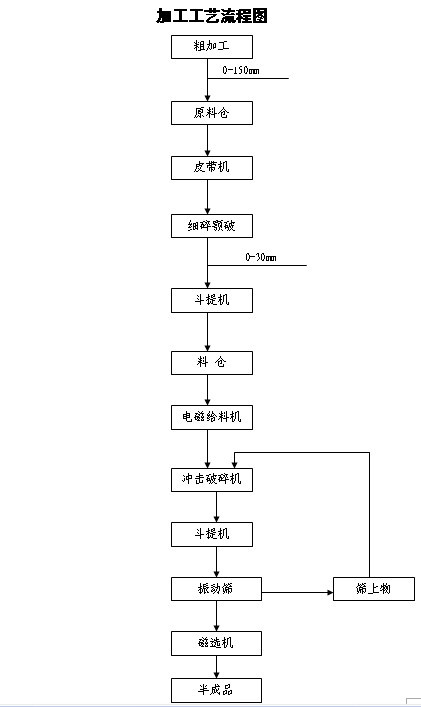
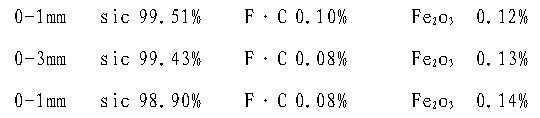
Angle Valves,Toilet Angle Valve,Brass Angle Valve,Bathroom Angle Valve
JIAHAOJIA SANITARY WARE INDUSTRY CO., LTD. , https://www.gagalfaucet.com