Ultra-high speed aluminizing technology developed for anti-supercritical water oxidation by metal
Thermal power generation accounts for 70% to 80% of power generation in China in the past three years. Since the first supercritical large-scale power station was built in 1995, the ultra-supercritical clean coal-fired power station has become the mainstream of thermal power in China. The 700oC ultra-supercritical thermal power generation technology plan is currently being implemented to further increase the efficiency of power generation and reduce CO2 emissions. Its target parameters are: pressure ≥ 35MPa, temperature ≥ 700oC. The improvement of the boiler operating parameters and thermal efficiency of heat generation has significantly increased the requirements for the oxidation resistance of supercritical water on the inner wall of the heat-resistant steel pipeline in the high-temperature section of the boiler. The experience of more than 20 years of power plant operation shows that the lifespan of traditional heat-resistant steel in supercritical power plants is much lower than that of subcritical power plants. The reason is that chromium oxide films are more prone to spalling and volatilization in supercritical water environments, resulting in the rapid consumption of Cr alloy elements. Catastrophic oxidation occurs. Two schemes have been proposed internationally, one is aluminum-containing heat-resistant steel and the Other is low-temperature aluminizing of pipes. So far, these two schemes have not been applied on a large scale. The main reason is that the aluminum-containing heat-resistant steel has insufficient processing and welding properties, and low-temperature aluminum penetration is difficult to avoid cracks. The “Coatings for Supercritical Steam Cycles†(SUPERCOAT) research project in Europe shows that the low-temperature aluminizing layer is a multilayered intermetallic compound brittle phase layer, and the coating structure and coating thickness are very sensitive to the heat diffusion temperature. Therefore, it is very urgent to develop a new anti-supercritical water oxidation coating suitable for the inner surface of the heat-resistant pipe.
It is well known that the effect of an electric field can cause a significant increase in the rate of atomic migration in metallic materials. Inspired by this phenomenon, Shen Mingli, an associate researcher of the High Temperature Protective Coatings Research Group at the Institute of Metal Research, Chinese Academy of Sciences, proposed the idea of ​​using eddy current electromigration to accelerate the alloying of metal surfaces in order to achieve ultra-high speed controllable aluminizing on the surface of large components. Experiments have shown that pulse current is applied to the sample (Fig. 1). Using joule heating of the current and surface eddy current electromigration effect, the surface of the heat-resistant steel coated with an aluminized slurry can be grown in 10 minutes (~900oC). Good toughness ~35μm FeAl or FeCrAl layer (Fig. 1e). The electromigration effect changes the diffusion mode and promotes the external diffusion of iron atoms. The nominal diffusion coefficient is more than ten times that of conventional methods. To obtain similarly porous layers, the traditional method requires several hours and higher temperatures, but long. Time high temperature treatment will seriously deteriorate the mechanical properties of the matrix. For the actual size of the heat-resistant steel pipe, the conventional process requires only several hours of heating and heating, and the technology still takes only a few minutes to achieve super-high-speed aluminizing. In addition, experiments have shown that, at higher current densities, a plastic solid-solute FeCrAl layer can be obtained in a shorter time (5 min) and the thickness of the permeation layer can reach ~35 μm (Fig. 2a), which cannot be achieved by conventional processes. The formation of such a solid solution penetrating layer is advantageous to avoid the problem of brittle cracking of the conventional aluminized coating. At present, by optimizing the aluminized slurry formula, under the same conditions, a FeCrAl layer of ~106 μm is obtained within 5 min (Figure 2b), and the growth rate is improved by nearly one order of magnitude. Experiments show that FeAl or FeCrAl coatings prepared by this method exhibit good Al2O3 film formation ability under high temperature steam conditions (Figure 3).
The eddy current electrophoretic accelerated aluminizing technique is expected to solve the problem of supercritical water oxidation of heat-resistant steel pipes for supercritical boilers. In addition, due to its low cost and ease of operation, this technology can also be applied to the preparation of high-temperature protective coatings for chemical pipeline components. This method has been authorized by the national invention patent, and related research work has been publicly published in Nature Communications ((2016) 7: 13797. doi:10.1038/ncomms13797, Shen M, Zhu S, Wang F, A General strategy for the ultrafast surface modification of metals). The study was funded by the Youth Science Foundation project (51301185). At present, it is planned to cooperate with related units to conduct research on industrial applications.
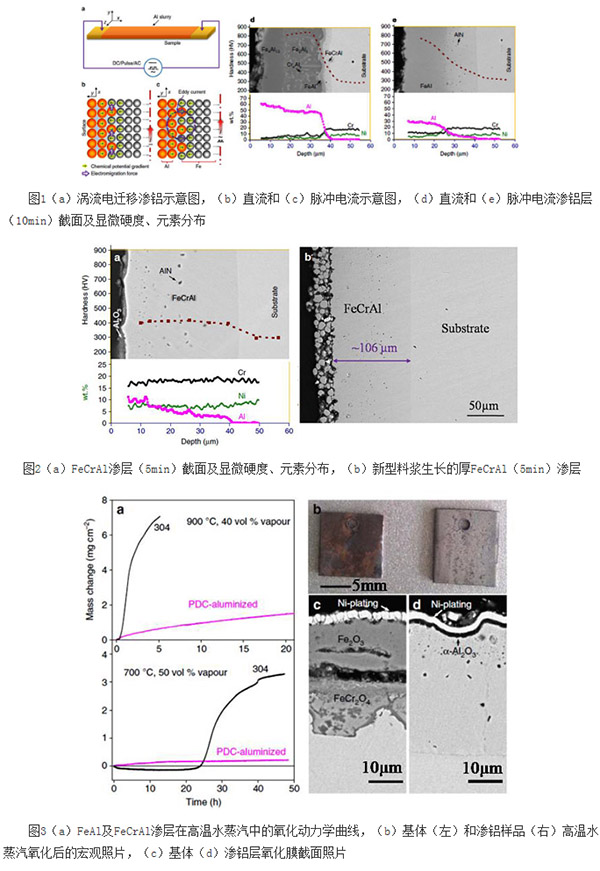
FUXIBIO Ffp2 Mask manufactured by Careable biotechnology Co.,Ltd
- High filtration Efficiency
- In Chinese PPE Export Whitelist
- Universal CE NB2163 Certification
- Low Breathing Resistance: Flow Rate≥95 L/Min
- Real FFP2 Standard: Test agent in (≤3μm) DOP, Penetration≤6%
- ISO9001 Quality Management System Certificate
Careable biotechnology, Ffp2 Approved Face Mask,Ffp2 Approved Mask Online,Ffp2 Approved Mask,Ffp2 Approved Face Mask Online
CAREABLE BIOTECHNOLOGY CO,. LTD , https://www.careablemask.com