Design of self-made honing equipment for machining wind turbine generator stator bracket locking hole
2020-07-28 04:12:55
The 2.0MW wind turbine developed by a design unit is currently the best-selling generator set in the domestic wind power industry. The stator bracket is a key component of the generator, with a diameter of about 4.5m and a weight of about 5.5t. For such large structural parts, The position tolerance of the locking hole at the locking device is φ0.3mm, the hole inner diameter tolerance is φ240+0.04 +0mm, the hole depth is 400mm, the surface roughness value is Ra=3.2μm, the verticality is 0.03mm, and the processing is difficult. , often appear to be out of tolerance. When machining the locking hole of the stator bracket, when the CNC gantry boring and milling machine is used to install the coarse and fine boring tools respectively, the shank sticks out for a long time due to the limitation of the workpiece structure, and the wall of the locking hole is rough and the dimensional accuracy in the hole often occurs. Poor problems, such as taper, bell mouth or waist drum, etc., combined with machine tool performance, tool characteristics and workpiece and hole characteristics, by controlling the processing parameters, replacing the fine tools, etc., in order to improve the processing quality of the hole, but always Can not be effectively improved. By changing the process method, the dimensional tolerances after the fine boring are adjusted, and the self-made special honing equipment is used for finishing processing to meet the dimensional accuracy and surface roughness requirements of the pattern, which satisfies the production needs and greatly improves the production efficiency.
Design idea
In order to reduce the surface roughness value of the locking hole and ensure the dimensional accuracy of the hole, it is not always effective to improve the processing quality of the hole by using a fine boring tool or the like. The idea of ​​transformation is to install the honing head on the gantry milling spindle to grind the inner hole. However, the self-made honing head needs to be connected with the shank on the gantry milling machine. The cutter head is heavy, the worker is difficult to operate, and at the same time, the gantry milling is occupied. Equipment station. In order to complete the processing with high efficiency, low cost and quality, a small-scale honing equipment is built and mounted on the workpiece for processing.
The honing machine is a grinding machine that hones the surface of the workpiece by using a honing head, and is mainly used for honing the workpiece hole in the manufacturing industries of automobiles, tractors, hydraulic parts, bearings and aviation. There are two types of honing machines: vertical and horizontal. The conventional honing machine fixes the workpiece on the machine tool. Because our company needs to process a hole in a certain part of a large part, the conventional honing machine can not meet the requirements. Based on the principle of honing, the personnel skillfully designed a honing head with a power unit to be mounted on the workpiece for processing.
2. Design principle
According to the characteristics of the workpiece, it is necessary to make a vertical honing head to reciprocate up and down, and complete the grinding process of the locking hole of the stator bracket (see Figure 1), as shown in Figure 2. The new honing machine mostly adopts a hydraulic expansion and contraction honing head, and the honing head embedded with the oil stone is rotated by the vertically disposed main shaft, and the vertical reciprocating feeding motion is driven by the hydraulic device. During the machining process, the whetstone of the honing head is fed radially under the action of the expansion and contraction mechanism, and the workpiece hole is gradually processed to the required dimensional tolerance and surface roughness. The design idea is to install the honing head on the base with the guide rail. The pedestal is placed on the workpiece. There may be a few millimeters of error between the honing head and the workpiece locking hole. The upper end of the honing head is two thousand. The transition joint is connected to the joint, so that the honing head automatically adjusts the universal joint under the pressure of its own weight and oil pressure, so that the honing head still moves downward along the original locking hole, and the grinding process can be completed, and the honing head can be solved. The problem of locking the hole alignment.
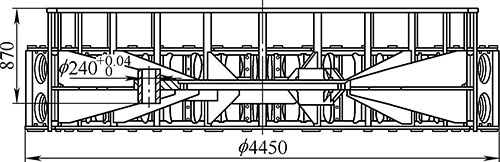
Figure 1 stator bracket
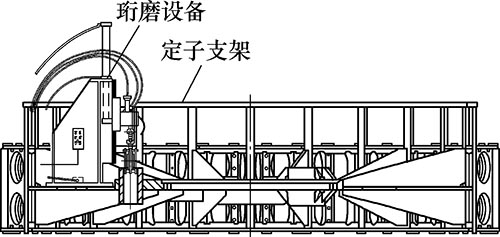
Figure 2 Schematic diagram of honing
3. Design, production and debugging
According to the above ideas and theoretical principles, combined with the size of the workpiece, the dimensions and parameters of all the components of the honing equipment (see Figure 3) are designed. The main components are described below.
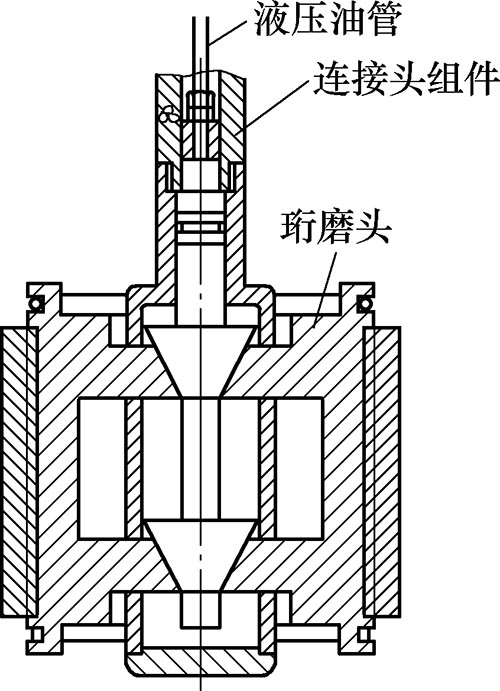
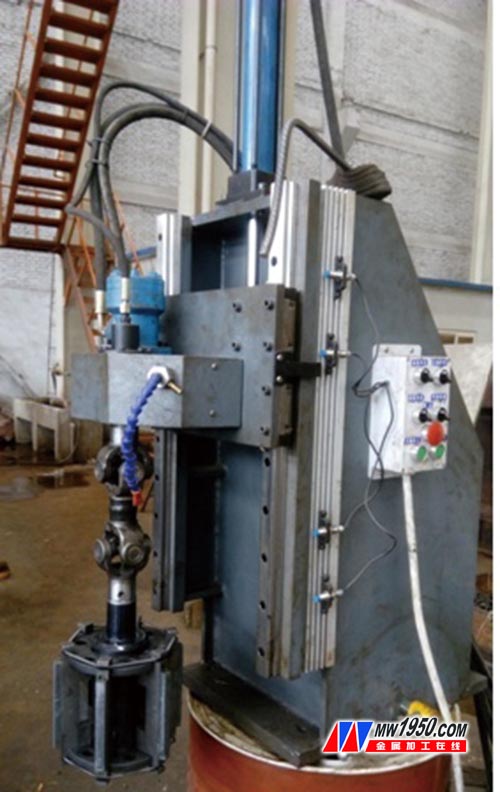
Figure 3 Schematic diagram of the honing equipment
(1) Honing head. The honing head is an important component of the honing equipment, which is responsible for the processing of the hole, and its working performance plays an important role in the dimensional tolerance and surface roughness value of the hole processing. It adopts the conventional structural form, which consists of a grinding head body, a stone stone, a stone stone seat, a guide strip, a spring and a cone expansion core. When the expanding core cone moves, the oil stone can expand or contract. The speed is designed to be 40r/min. The diameter of the bore is 240mm. The cutting speed can reach 30m/min, which is in line with the reference value of the metal cutting manual. The oil stone is selected from 6 pieces and the length is 160mm. The working stroke of the honing head is roughly calculated according to the length of the oil stone, which can be used as the setting of the driving parameters of the subsequent hydraulic device. After the honing head is finished, it needs to be rounded once to ensure the dimensional tolerance and roundness requirements.
(2) Universal transmission. The universal joint transmission is composed of a universal joint and a transmission shaft. The universal joint is a mechanism for realizing variable-angle power transmission, and is used for changing the position of the transmission axis direction, and the transmission shaft is driven by a hydraulic motor to realize a rotary motion.
(3) Connecting the sliding device. The component for coupling the universal joint device and the honing head as a whole can reciprocate up and down in the main tank by the action of the hydraulic cylinder.
(4) Hydraulic drive unit. The above three parts are driven to reciprocate up and down under the action of hydraulic oil, and the hydraulic driving parameters are calculated according to the working stroke of the honing head.
(5) Main cabinet. The main box body is a welded box body, and the dovetail type slide rail is connected in the vertical direction of the outer surface of the box body, and carries the load of the motion mechanism. The sliding device and the main shaft are driven by the hydraulic device to perform the upper and lower reciprocating grinding movements. Install a magnetic suction cup device under the cabinet. After the whole honing equipment is lifted onto the workpiece and laid flat, the hand pulls the magnetic suction cup handle to rotate, so that the box body is firmly fixed on the surface of the workpiece.
According to the design drawings, the assembly is completed. By continuously debugging the equipment, the parameters such as the rotation speed and the feed are adjusted to meet the requirements of use, and the inner hole is ensured to meet the pattern requirements after processing. Through trial processing, the self-made equipment fully meets the processing needs, and has now entered the normal production stage, achieving the expected results.
4. Conclusion
The partial deep hole is processed on the large structural parts, and the self-made vertical small honing equipment is designed to meet the product design and use requirements, reduce the manufacturing cost, improve the production efficiency, and have certain promotion value.
references:
[1] Zhu Xinghua. Principles of Grinding [M]. Beijing: Mechanical Industry Press, 1998.
[2] Mechanical Engineering Manual Editorial Board. Mechanical Engineering Handbook [M]. 2nd ed. Beijing: Mechanical Industry Press, 1993.
Old salts of inorganic or inorganic compounds, minerals, in the biological cells typically accounts for 1% to 1.5% of fresh weight, the human body has been found more than 20 kinds, including a large number of elements have a Ca Ca, P, P, K K, S S chlorine, Na, Na, Cl, Mg Mg, trace elements have a Fe of iron, zinc, zinc, selenium Se, Mo Mo, fluorine cobalt chromium, Cr, Co, iodine I F, etc.
Inorganic Salt,Magnesium Sulphate,Sodium Hexametaphosphate,Ammonium Bisulfite
SHANDONG ZHISHANG CHEMICAL CO.LTD , https://www.zhishangchemical.com